Electrostatic Paper Feeder
Keywords: Electrostatic force, Electrostatic actuator, Paper feeder, Paper transportation
Movie | QuickTime, 514KB |
The equipment appeared in this video is a bit different from one in this article. |
Introduction
We have been developing several types of high-power electrostatic motor.
Among those motors, Pulse Driven Induction Electrostatic Motor[1], which consists of stator with electrodes and high-resistivity slider, can be used as electrostatic paper feeder[2].
Now, almost every printer and copier utilizes sets of rollers and electro-magnetic motors as its paper feeding mechanism.
However, such paper feeding mechanism has such defects as:
- It requires reduction gears that makes whole system large,
- It drives paper using friction force, therefore, it is not suitable for low-friction papers,
- Whole driving force acts on small area where the roller and paper get contact, therefore, sometimes it can break thin papers.
To solve those problems, some researchers have proposed to utilize ultrasonic motors for paper feeding mechanisms[3-5].
Utilizing ultrasonic motors is effective for making compact paper feeding mechanism, however, it still has the same friction problem as conventional mechanisms.
In this article, we introduce novel electrostatic paper feeding mechanism that can solve those mentioned problems.
Principle
The electrostatic paper feeder employs Pulse Driven Induction Electrostatic Motor[1].
The principle of the motor is described in this page.
Surface resitivity of papers
In Pulse Driven Induction Electrostatic Motor, operation stability depends on surface resitivity of slider (slider is paper, in this case).
If surface resitivity of the slider is too low, the slider surface charges will easily disappear when the stator voltages are switched.
This leads to unstable operation.
On the other hand, if surface resitivity is too high, it will take too much time to induce charges on slider surface.
Our analyses tell us that surface resitivity should be between 1013 [ohm] and 1015 [ohm].
Whereas, surface resitivities of papers are sensitive to humidity and varies from 109 to 1016 [6,7].
Figure 1 shows the result of surface resitivity measurements.
We measured resitivity of PPC (Plain Paper Copier) paper, magazine paper, and tissue paper.
Their surface resitivity is a little bit lower than ideal resitivity of our electrostatic motor.
Especially, the surface resitivity of PPC paper is too low.
This is because, it is coated with conductive materials to prevent paper jam and to obtain high quality pictures (to obtain high quality pictures by electric copiers or by laser printers, the surface resitivity should be between 109 and 1013 [7,8]).
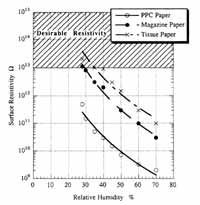 |
Figure 1: Surface resitivity of papers |
Feeding experiments
We carried out paper feeding expeiments using a electrostatic paper feeder shown in figure 2.
The effective electrode ares of this feeder is 265mm x 285mm.
Electrode pitch is 1mm.
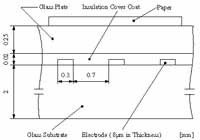 |
Figure 2: Schematic view of electrostatic paper feeder |
Feeded papers in the experiments were japanese paper, magazine paper, printer form (for dot impact printer), and PPC paper.
The size of every sheet of paper was 50mm x 50mm.
Wights are 0.33g (japanese paper), 0.89g (magazine paper), 0.82g (printer form), and 1.16g (PPC paper).
Fricition coefficients are 0.1-0.2 for japanese paper and 0.2-0.3 for the others.
Driving voltage was ±1kV.
For charge process, we applied [+,-,0] voltage pattern for 80ms.
For driving process, we applied [-,+,-] voltage pattern for 20ms.
Figure 3 shows a plot of moving length of each paper in one driving step.
Temperature was 26 °C.
Japanese paper, magazine paper, and printer form was feeded in low humidity.
However, PPC paper was not feeded even at 15%RH (relative humidity).
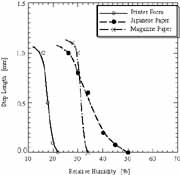 |
Figure 3: Step length vs. humidity |
Next experiments were carried out by using double-side feeder as shown in figure 4.
The gap between bottom plate and top plate was set at 0.2mm for magazine paper, and at 0.1mm for the others.
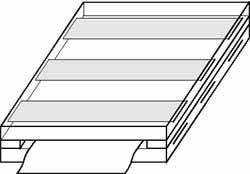 |
Figure 4: Double-side feeder |
Figure 5 shows a result obtained using the double-side feeder.
The plot curves of japanese paper, magazine paper, and printer for shifted to higher humidity side compared to the result shown in figure 3.
PPC paper, which could not be feeded in single-side feeder, was successfully feeded in this feeder.
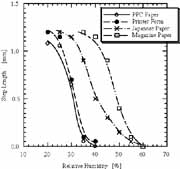 |
Figure 5: Result of double-side drive |
Features
The merits of utilizing the electrostatic paper feeder are:
- Compactness,
- Ability to drive low-friction papers,
- Ability to drive very thin papers.
Defects of this feeder are:
- Small driving force,
- Sensitiveness to humidity.
See also
References
[1] S.Egawa, T.Niino, and T.Higuchi, "Film actuators: Planar Electrostatic Surface-Drive Actuators", Proc. 1991 IEEE Workshop on Micro Electro Mechanical Systems, pp. 9-14 (1991)
[2] T.Niino, S.Egawa, T.Higuchi, "An Electrostatic Paper Feeder", Journal of the Japan Society for Precision Engineering, Vol. 60, No. 12, pp. 1761-1765 (1994) (in Japanese)
[3] Y.Tomikawa, T.Nishitsuka, T.Ogawsawara, and T. Takano, "A Paper of Card Forwarding Device Using a Flat-Type Ultrasonic Motor", Sensors and Materials, Vol. 1, No. 6, p. 359- (1989)
[4] Yoshida and Shimizu, "Application of ultrasonic motor to card feeder", Tokin Technical Review, 16, p. 36- (1990) (in Japanese)
[5] T.Oda, Y.Kamiya, and S.Okabe, "Study on Sheet Escape and Feeding Mechanism using Ultrasonic Vibration (1st Report) -Design Concept and its Experimental Investigation-", Journal of the Japan Society of Precision Engineering, Vol. 58, No. 3, p. 445- (1992) (in Japanese)
[6] T.E.Cooprider: "Resistivity Testing Methods for Conductive Base Paper", Tappi, Vol. 51, No. 11, p. 520- (1968)
[7] Matsuda, Electrophotographty (the society journal), Vol. 28, No. 2, p. 160- (1989) (in Japanese)
[8] Sakamoto, Electrophotography (the society journal), Vol. 14, No. 1, p. 2- (1975) (in Japanese)